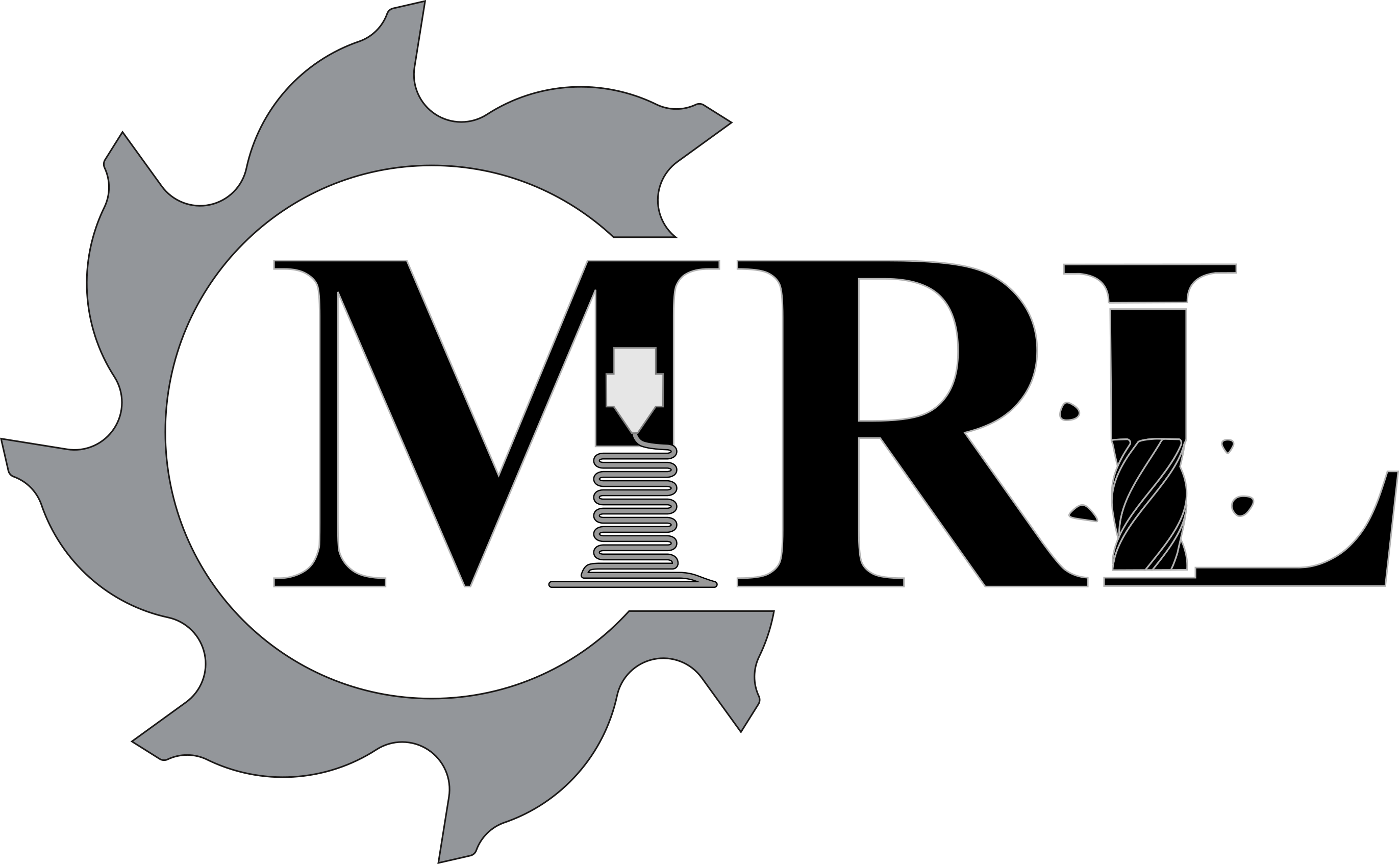
Machining Research Laboratory
Welcome to the Machining Research Laboratory in the Faculty of Engineering and Applied Sciences at Ontario Tech University. At MRL research focuses on developing and improving techniques in subtractive and additive manufacturing.